Advanced Asphere Processing
Complex Aspheres with Exceptional Surface Accuracy to λ/4
Mid-spatial frequencies (MSFs) affect your optical system's performance by scattering light, which reduces image contrast and overall image quality.
LaCroix's aspheric machinery uses unique kinematics to reduce MSFs and improve form error, giving you the image quality and performance your project demands.
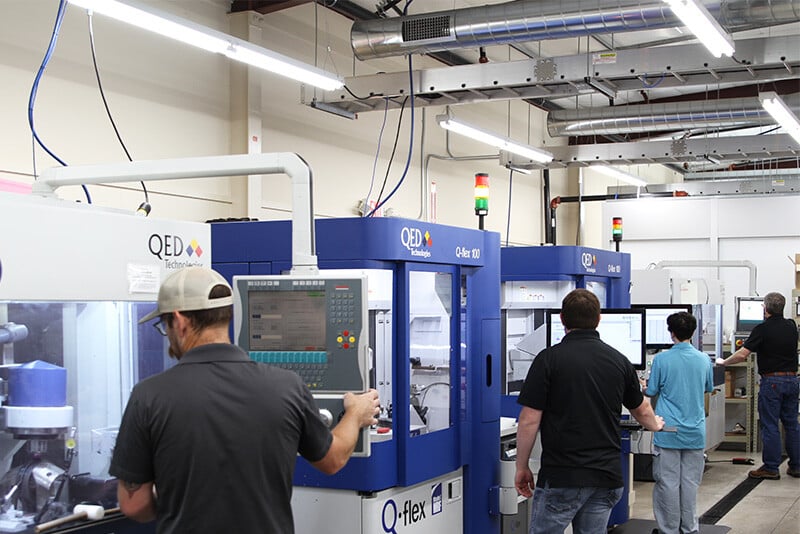
MRF Cell
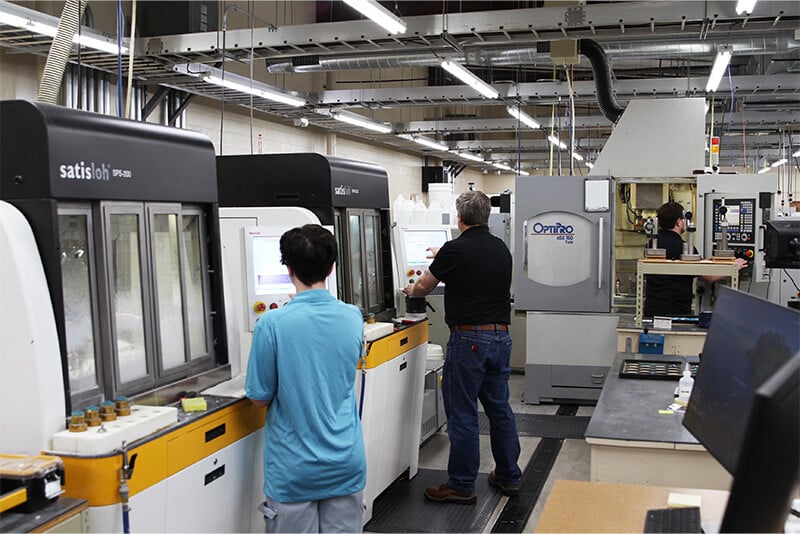
Asphere Cell
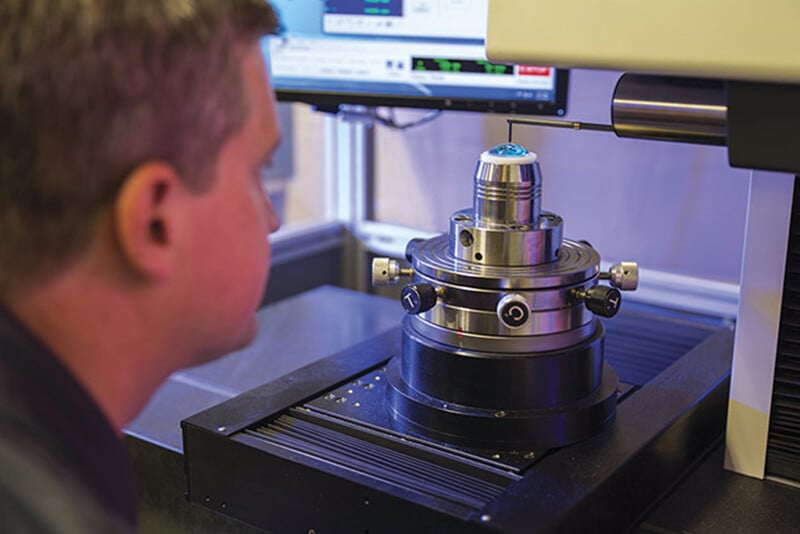
2D Profilometry
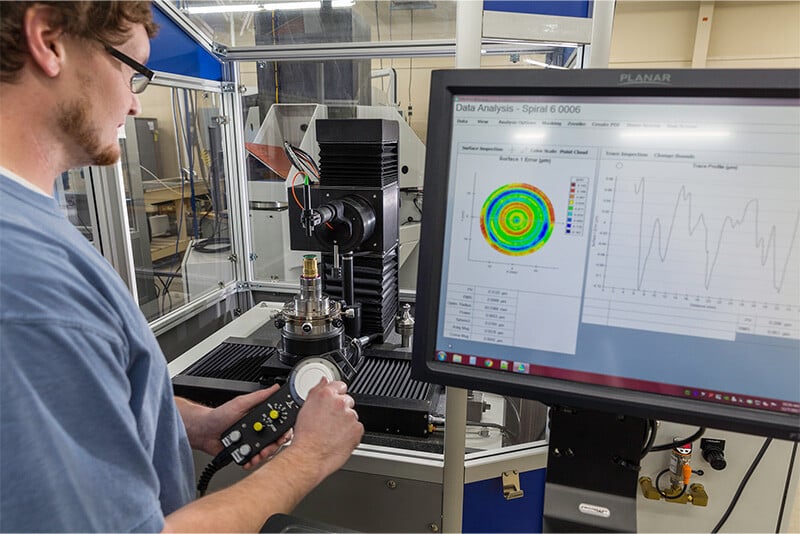
3D Profilometery
Aspheric Manufacturing Equipment
- Satisloh SPM-200
- OptiPro eSX 150
- Satisloh SPS-200
- Satisloh SPS-125
- OptiPro UFF 300
- QED Q22-Y
- QED Q-Flex 100
- OptiPro OptiTrace 5000 Profilometer
- OptiPro UltraSurf 4X 300 3D Profilometer
- Taylor Hobson PGI Optics Profilometer
Manufacturing Aspheres
We begin processing aspheric lenses by designing a near net-shaped optical glass blank and then grinding a best-fit sphere onto the surface. From this point, the initial aspheric profile is ground onto the lens using one of our advanced aspheric grinders.
Metrology is then used to measure the surface of the asphere and characterize all deviations from its theoretical form. This information is then used to correct and reduce form error on the aspheric surface. A fine grind is performed to minimize sub-surface grinding damage and prepare the asphere for polishing.
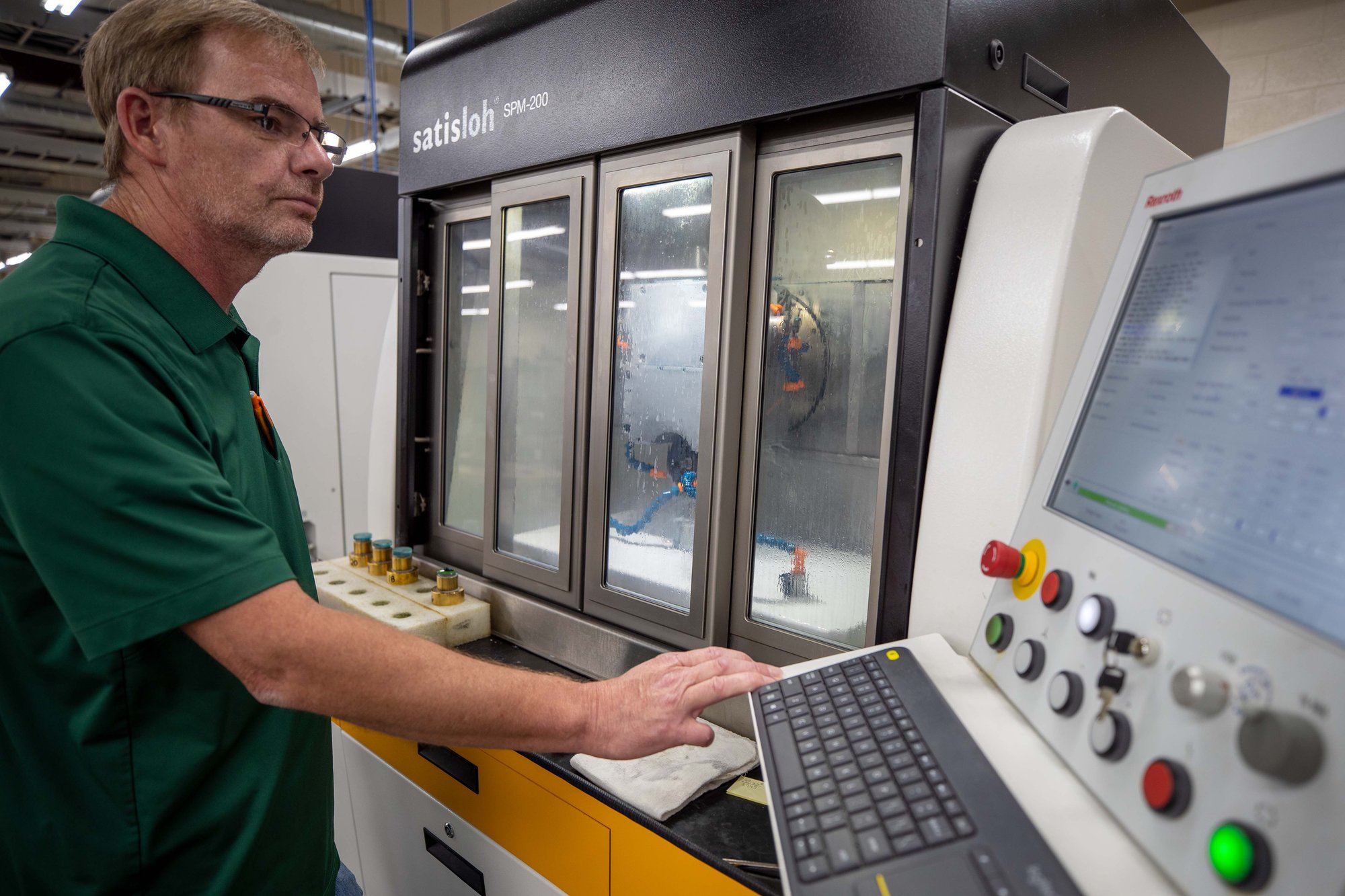
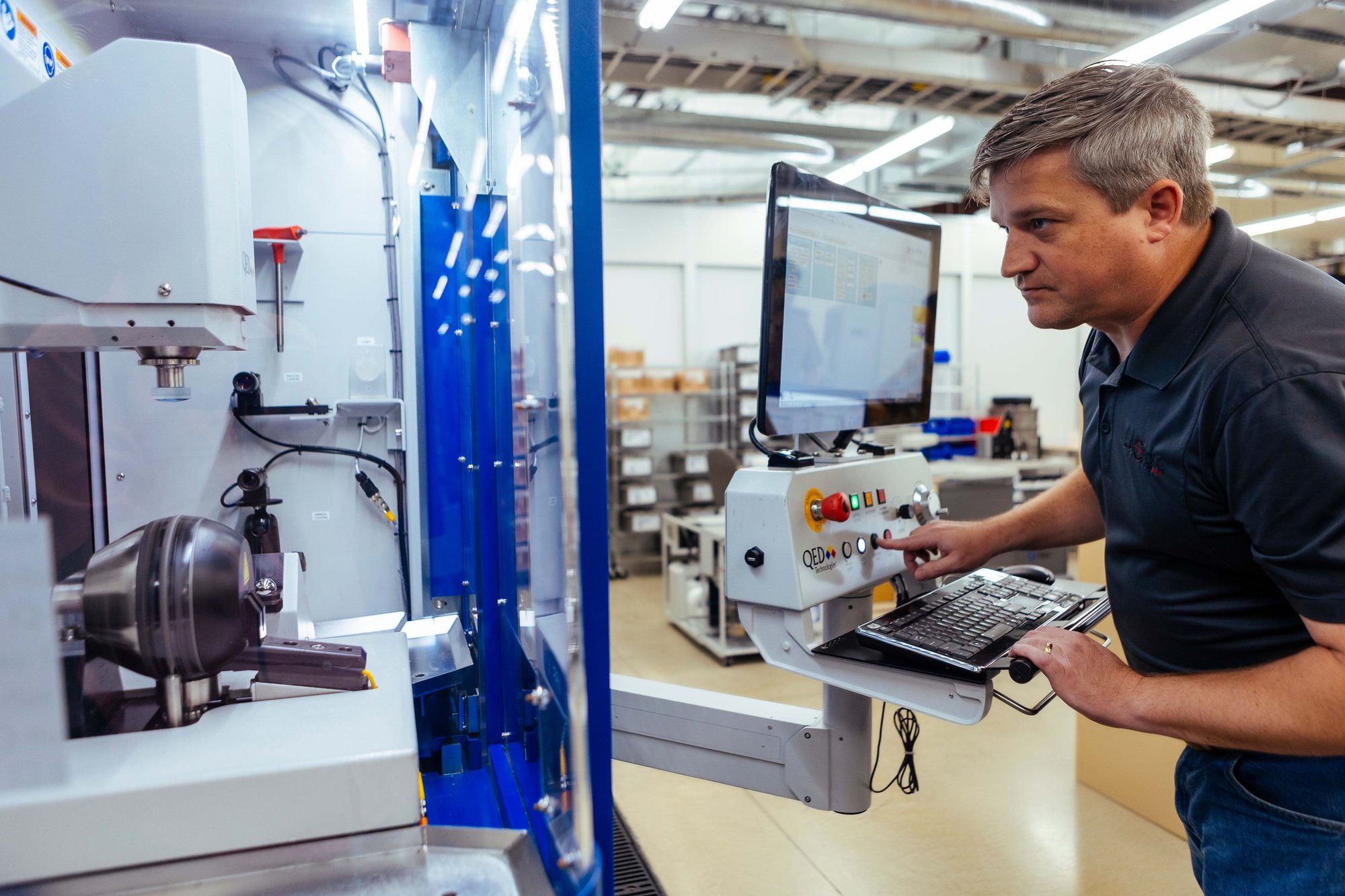
The aspheric lens is then greyed out, removing the subsurface damage. This begins a corrective feedback loop between metrology and the aspheric polishers.
When necessary, a finishing process is performed using MRF to reduce form and slope error.
Magnetorheological Finishing (MRF)
MRF uses a magnetically-sensitive fluid to create a moving ribbon to polish optics. The fluid is manipulated using a magnetic field to adjust the viscosity and thus the removal rates. The lens is then pulled across the ribbon in either a spiral or raster path.
MRF can produce significant increases in quality. Spherically, λ/20 surfaces can be achieved. Aspheric surfaces can reach λ/4, with reduced mid-spatial frequency errors.
Attribute | Standard | Precision | High Precision |
Form Error (microns) | ±1 | ±0.5 | ±0.25 |
Slope Error (µm/mm) 1mm Integration Window | 0.5 µm/mm | 0.25 µm/mm | 0.1 µm/mm |
Frequency Errors | Specify Spatial Frequency Bands as Necessary | ||
Metrology | 2D & 3D Metrology | ||
Diameter (mm) | 10-200mm |